Woods & CONSTRUCTION
WOOD, THE ESSENTIAL INGREDIENT IN EVERY ACG
Over the last 20 years have been accumulating a collection of different woods from all round the world. I think it is fair to say this got out of hand for a while but I have things under control now. Anyway this means I have a lot of woods for you to choose from. The best way to get an idea of what is possible is to look through my past work. This is without doubt better than a list of woods, it would be long and not that helpful.
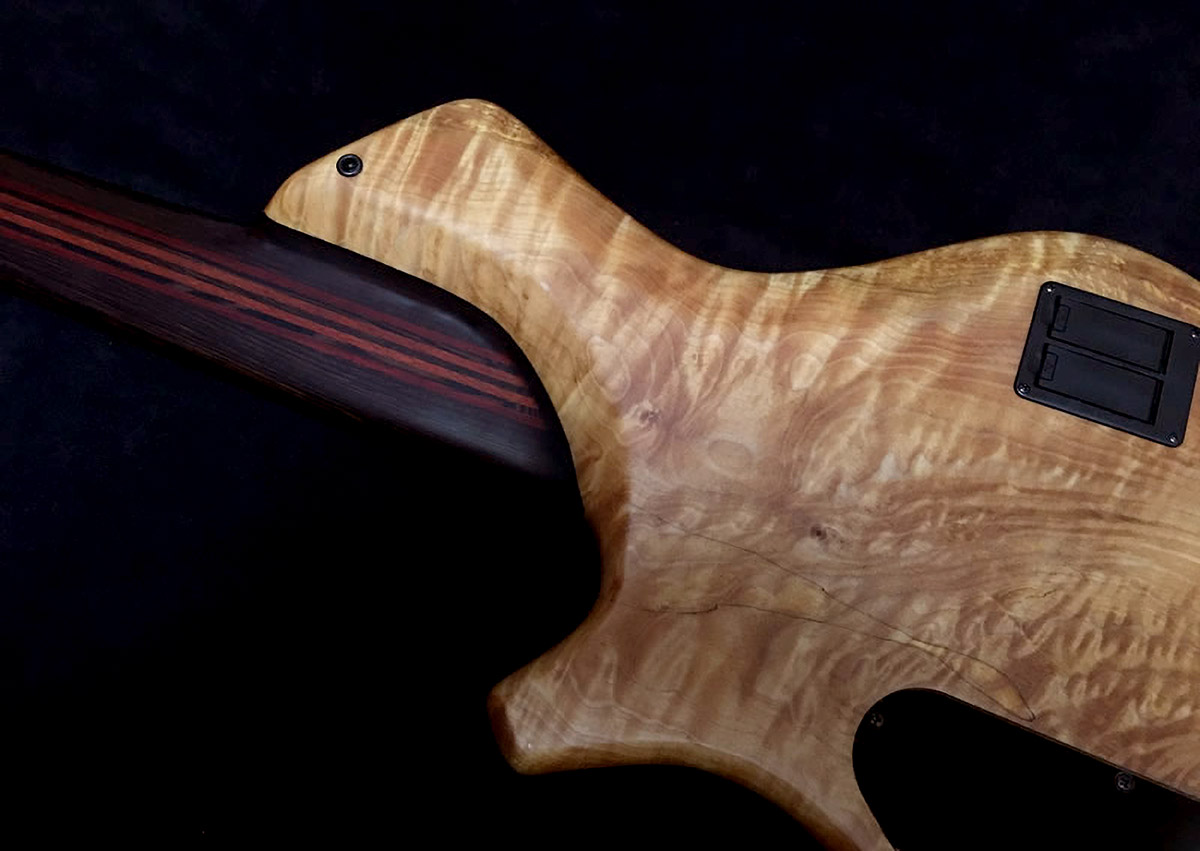
ART & AI WOODS
ART (Acrylic Resin Treated)
AI (Acrylic Impregnated)
I started using AI woods pretty much straight away mainly for fret boards. I could see no down side to them 20 years ago and this is still very much the case today. The ART woods came along a bit later and have brought a whole new world of colours being dyed and dual dyed. Since the process cannot be controlled where dye takes or does not take produces interesting and unique tops. The next step was ART/Hybrid tops. These combined ART boards with epoxy resins. This further increased the complexity of the colours and textures possible in a top wood.
For 20+ years I worked with one guy on all the AI/ ART and Hybrid tops. We were friends even though we never actually meet. We tried several times but never managed it. Larry Davies sadly passed away in April 2024. I lost a friend and someone that has been with ACG since the day it started.
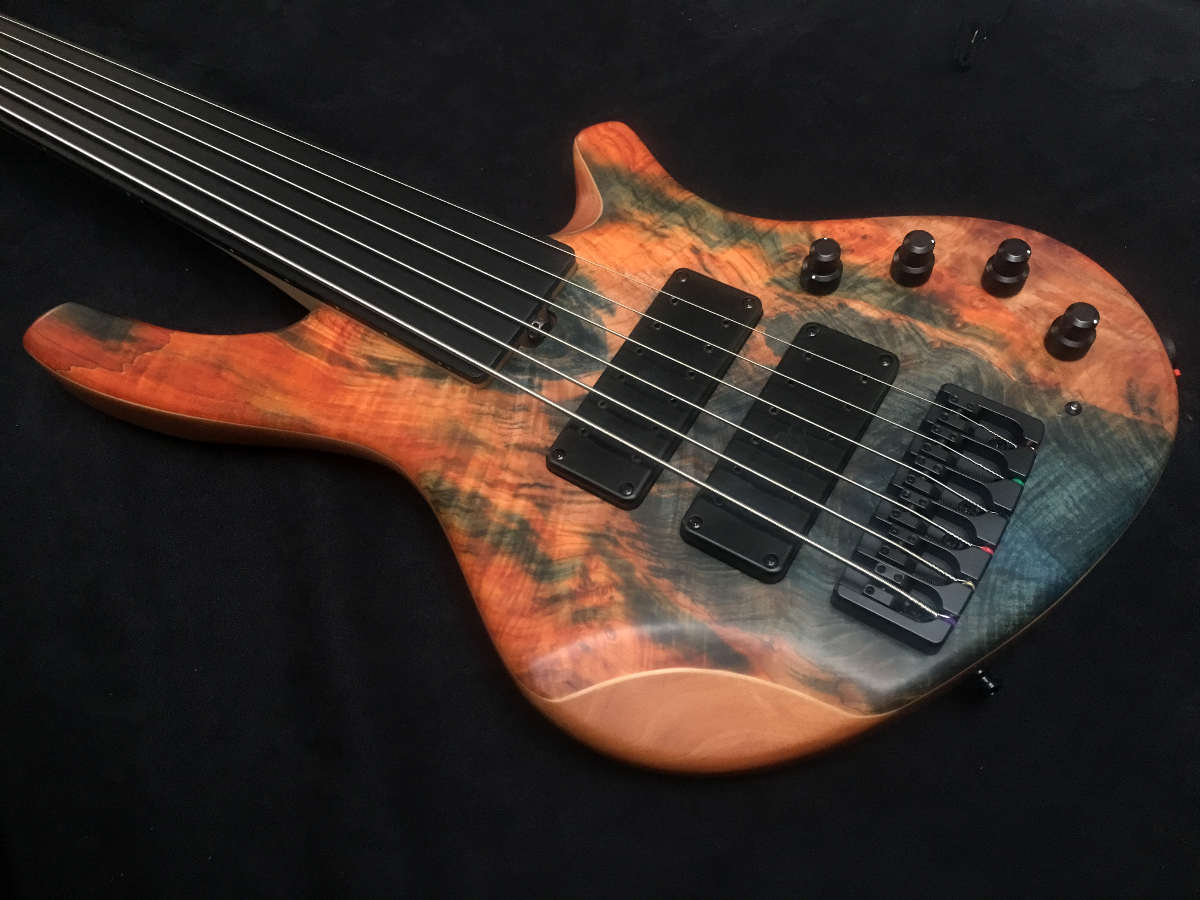
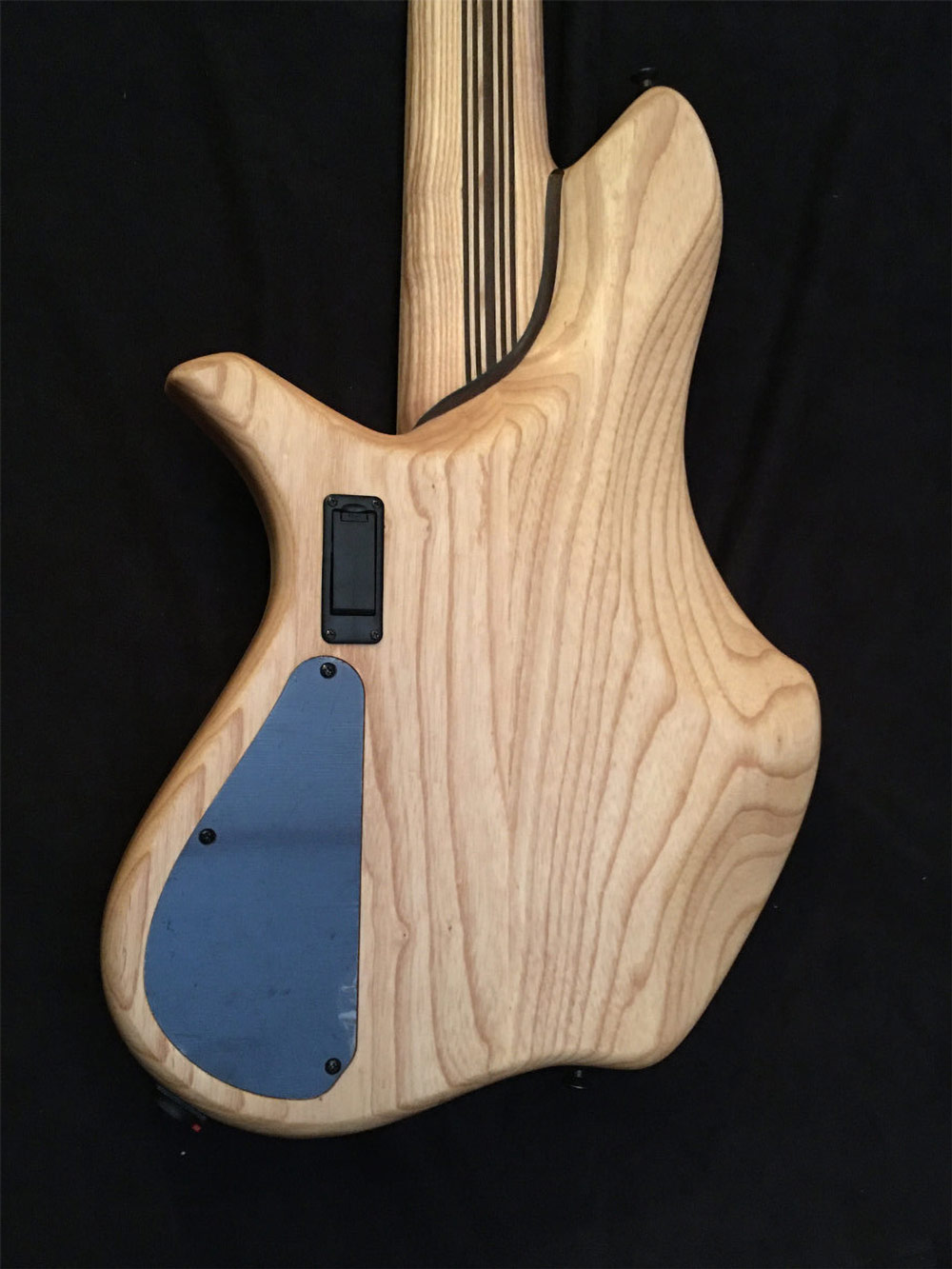
NECK CONSTRUCTION
Probably the most important element of any build.
All my bass and guitar necks are constructed using a multi-laminate method, I find this the best way to construct a stiff and stable neck.. I build set neck (neck glued into the body) and bolt-on necks.
I like to keep the wood that is destined to be necks for at least 6 months before cutting them into the laminates. Once cut into standard neck laminate sizes, I leave them again for as long as possible before making them into necks. This allows the woods to settle, and if they are going to move, this is when it happens.
All neck woods are dated when they are cut and put together in the rack. This allows me to keep track of each batch in the wood store. The laminates are then selected, and the grain in each is arranged to give a stable neck construction. Once glued, the laminates are left to settle until the neck blank is planed to size. Clearly this is not a quick process, but I believe it is worth the effort.
Bolt-on necks use steel inserts in the heel. To attach the neck to the body, I use M5 Allen bolts that sit in a custom-made aluminium cup washer. Set necks are glued into an elongated neck pocket, which extends to the neck pickup. This length increases the gluing surface area for the neck.
The remaining elements of the neck are the headstock and fingerboard, carbon and trussrod. I use a scarf joint on all angled headstocks. This reduces waste and makes for a very solid headstock. The actual joint is hidden under the headplate, backplate and ears that are added to the headstock. All custom necks are further reinforced with two 6.35mm carbon rods on either side of the trussrod. This increases the stiffness of the neck and, in my opinion, helps reduce dead spots.
AI FRETBOARDS
Along with the usual fret board woods I have a large selection of Acrylic Impregnated Woods suitable for fingerboards. The proprietary process utilises a vacuum oven to infuse woods with acrylic monomers. This process ensures that resin is drawn through the entire board, and is not just a surface treatment. The acrylic not only stabilises the wood and increases its density and hardness, it also increases its resistance to movement caused by moisture. This process expands the choices for fingerboards. For example, it allows me to use the previously unsuitable Spalt Maple with great success.
I also use the acrylic impregnation process on traditional fingerboard woods, such as Mac Ebony. The process makes what is already a good board even better. Another advantage of the process is that it seals the wood, which, on a light-coloured fingerboard like Birdseye Maple, removes the need for a spray finish to stop the board getting dirty. This is ideal if you don’t like the feel of lacquer under you fingers.
Remember, I don’t use a manmade fingerboard like Diamond wood: this is a process that simply enhances real wood.
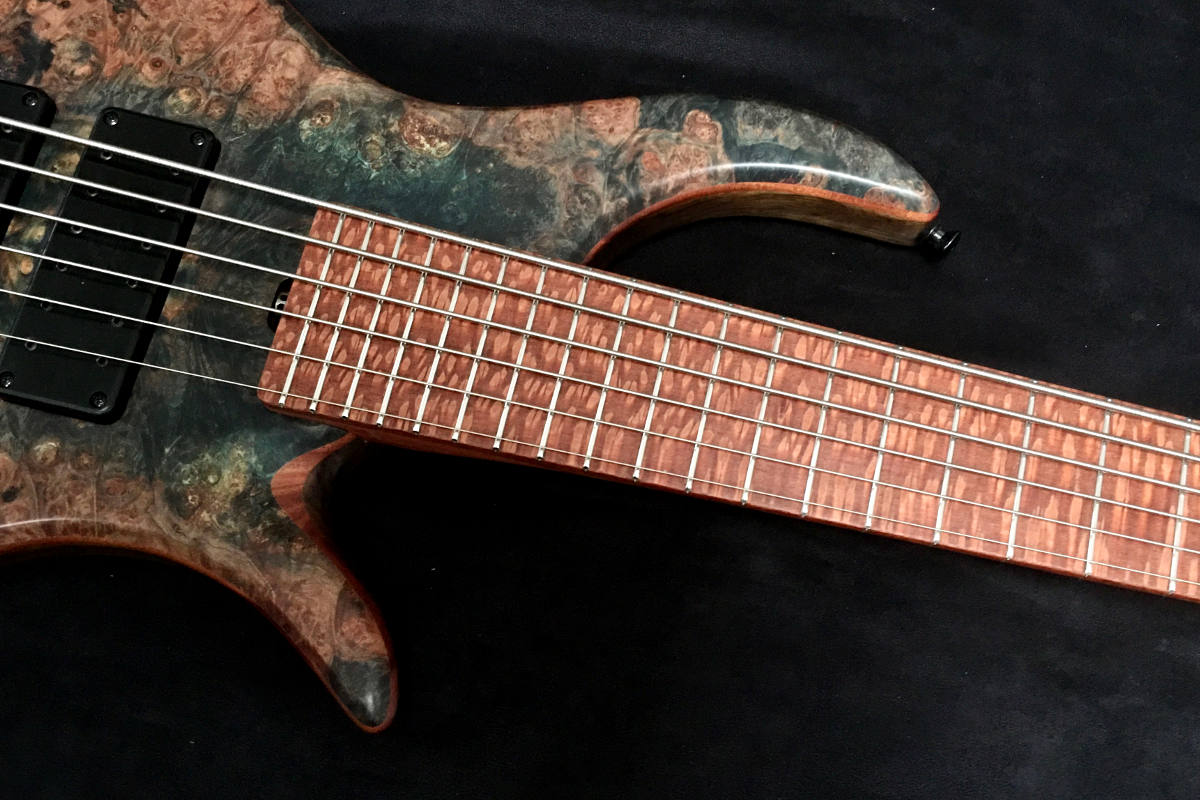
FINISHING
I have spent a lot of time perfecting my spray finish. A lot of experiments and failures later I feel I now have a consistent finish the way I want it. Not fully satin or a gloss it provides a very good tactile experience on the all important neck.
I also have my MLF (Minimum Lacquer finish) this is a grain textured finish with only a few coats of lacquer applied. I use this mainly on the Graft and Standard Series.
I also offer an oiled finish but only when suitable woods are chosen for the build. I mainly use the oil finish for the neck on the Graft and Standard Series but on occasion with the Custom Series.